Choosing the right cable carrier is crucial for ensuring optimal performance, safety, and durability in any industrial, automation, or robotics application. With a wide variety of cable carriers available in the market, it’s essential to choose the one that best meets your specific needs. In this guide, we’ll walk you through the key considerations and factors to help you select the perfect cable carrier for your unique application.
1. Understand Your Application’s Motion Requirements
The first step in choosing the right cable carrier is to assess the type of motion involved in your application. Cables are often used in environments where they need to move continuously or intermittently. The movement could be:
- Linear Motion: Straight-line movement, often found in automated machines or CNC systems.
- Rotary Motion: Movement around an axis, common in robotics and rotating machinery.
- Multi-Axis Motion: Combination of movements, typically seen in complex robotics or heavy machinery.
Knowing the type of motion your cables will experience helps determine the cable carrier’s design and material specifications.
2. Consider the Cable Carrier Size and Configuration
Cable carriers come in a variety of sizes, shapes, and designs. The size of the cable carrier depends on the number, size, and type of cables that need to be managed.
- Width and Height: The internal width and height should be sufficient to accommodate all cables while providing some extra space for flexibility and future expansions.
- Chain Type: Consider whether a closed or open chain design would work best. Closed chains offer greater protection to cables, while open chains offer easier cable management and maintenance.
Choosing the right size and configuration ensures that your cables move smoothly within the carrier, preventing wear and damage over time.
3. Material Selection for Durability
The material of the cable carrier plays a significant role in its longevity and performance. Cable carriers are made from a range of materials, including:
- Plastic: Lightweight, corrosion-resistant, and ideal for applications with lighter cables and less demanding environments.
- Steel: Stronger and more durable, often used in heavy-duty applications or where the cable carrier is exposed to harsh conditions.
- Hybrid Materials: Some cable carriers combine plastic and metal to take advantage of both materials’ benefits, providing strength with reduced weight.
The choice of material depends on your specific environment. If your application involves exposure to chemicals, high temperatures, or extreme conditions, opting for more robust materials is essential.
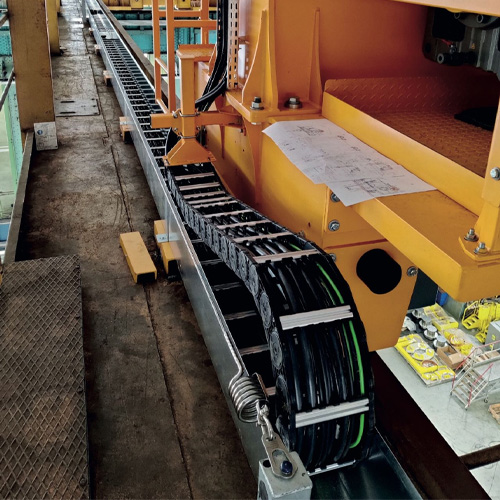
4. Evaluate the Environmental Conditions
The environment in which your cable carrier operates plays a key role in the decision-making process. Factors like temperature, humidity, exposure to chemicals, and physical stress must be considered to ensure the longevity and performance of the carrier and cables.
- Extreme Temperatures: If your application operates in high or low-temperature environments, opt for materials designed to withstand those conditions.
- Chemical Exposure: For environments with exposure to oils, lubricants, or harsh chemicals, choose a cable carrier made of corrosion-resistant or chemically resistant materials.
- Outdoor vs. Indoor: Outdoor applications may require a cable carrier with UV resistance and added protection against weather elements.
By choosing a cable carrier that can withstand the environmental conditions, you reduce the risk of damage to cables and increase the system’s overall lifespan.
5. Ensure Proper Cable Management and Flexibility
Cable management is one of the primary purposes of a cable carrier, but it should also allow for flexibility, especially in dynamic applications. To achieve this:
- Internal separators: These help organize cables within the carrier, preventing tangling and damage.
- Flexibility: If your system involves frequent starts and stops, ensure the carrier has the flexibility to handle repetitive motion without putting undue stress on the cables.
Opt for cable carriers designed with easy-to-open links for simple cable installation and maintenance. This feature significantly reduces downtime during repairs and upgrades.
6. Consider the Cable Carrier’s Weight and Load Capacity
If your cables are particularly heavy or the system involves significant weight-bearing tasks, the load capacity of the cable carrier becomes crucial. Heavy-duty cable carriers are designed to support greater weights, but they might come with a trade-off in terms of flexibility or size.
- Light-duty carriers are sufficient for smaller applications with low to medium cable loads.
- Heavy-duty carriers are designed for systems that require handling large, bulky cables or high-torque machinery.
7. Ensure Compliance with Industry Standards
For specific applications, especially in highly regulated industries like aerospace, automotive, or food processing, ensure that the cable carrier meets relevant industry standards and certifications. Compliance ensures safety and reliability in the system’s performance.
Look for certifications such as UL, CSA, or IP ratings, which specify the carrier’s suitability for particular environmental conditions.
8. Evaluate Maintenance and Accessibility
Ease of maintenance is another essential factor in selecting the right cable carrier. Over time, wear and tear can cause damage to cables or the carrier itself, requiring regular maintenance or replacement of components. Consider cable carriers that:
- Allow quick access: Choose models with openable links or flexible components to make inspections and repairs easier.
- Offer easy routing: Look for carriers that enable quick and easy installation of new cables or re-routing of existing ones, minimizing downtime during maintenance.
9. Budget and Cost Considerations
While cost shouldn’t be the only factor in selecting a cable carrier, it’s important to find a balance between performance and budget. High-quality materials and features such as easy accessibility, flexibility, and load capacity may come with a higher initial cost but could save you on long-term maintenance, replacement, and downtime costs.
Conclusion: Choosing the Right Cable Carrier for Your Application
Selecting the right cable carrier involves assessing a variety of factors, from the type of motion and environmental conditions to size, material, and ease of maintenance. By taking the time to carefully consider these factors, you can choose a cable carrier that will provide reliable cable management, enhance the longevity of your cables, and minimize downtime in your operations.
When selecting a cable carrier, always prioritize your application’s specific needs, and consider consulting with a professional to ensure that the solution you choose is the most efficient and cost-effective.